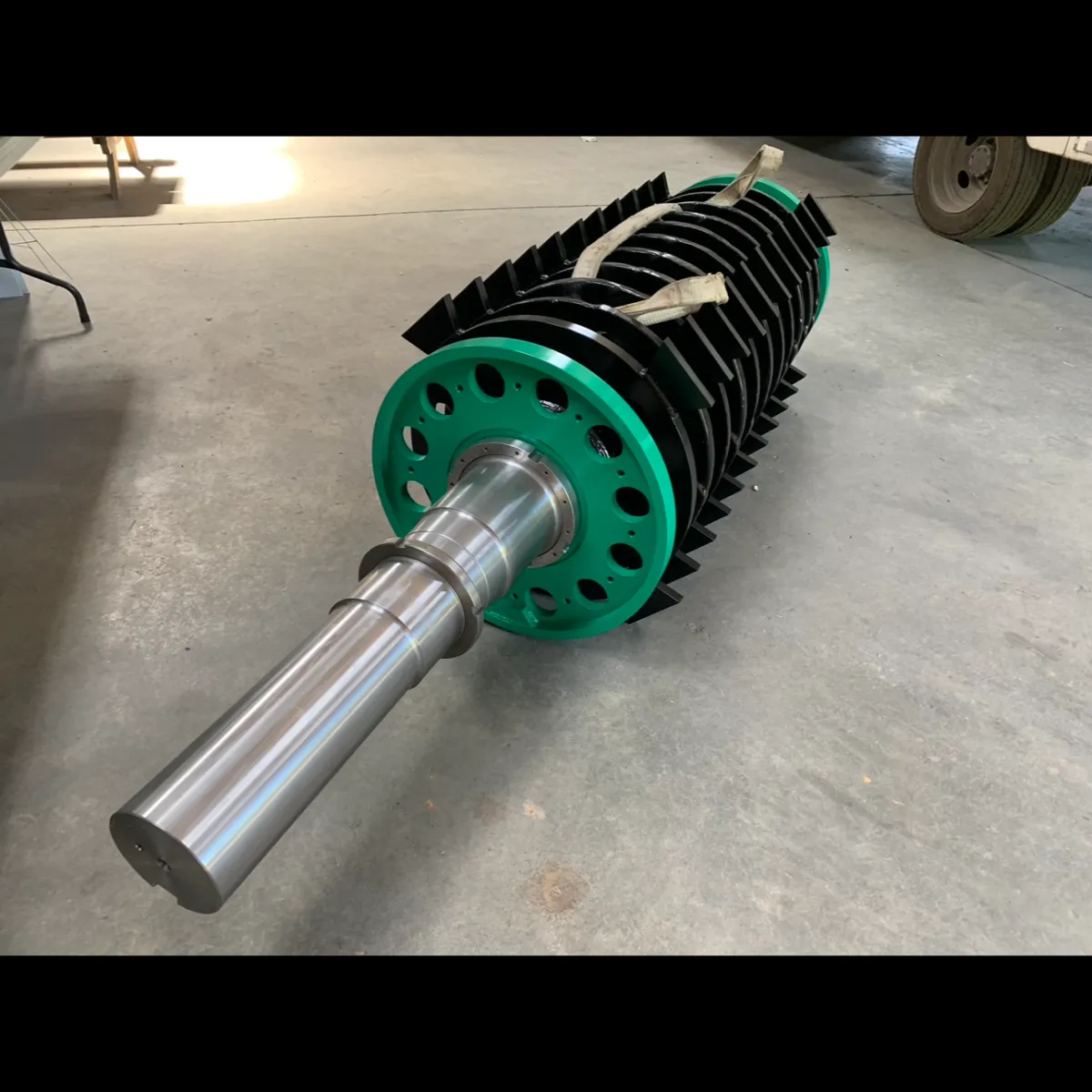
What Makes a Good Mining Maintenance Plan?
What Makes a Good Mining Maintenance Plan?
In the mining industry, equipment downtime is more than just an inconvenience — it’s a financial threat. From massive haul trucks and drilling rigs to loaders and crushers, mining operations rely on heavy equipment running efficiently every day. That’s why a solid mining maintenance plan isn’t optional — it’s essential.
A well-structured plan helps maximize equipment life, reduce unplanned downtime, boost safety, and ultimately improve operational profitability. In this article, we’ll break down the core elements of a good mining maintenance plan, key strategies to implement, and how to tailor your plan to meet the unique demands of your site.
Why Maintenance Planning Matters in Mining
Mining equipment operates under extreme stress. It faces abrasive materials, long operating hours, vibration, moisture, and environmental conditions that test durability daily. Without proper maintenance, equipment can fail suddenly, putting lives and production targets at risk.
An effective mining maintenance plan:
Reduces emergency breakdowns
Increases machinery lifespan
Improves safety and compliance
Enhances productivity through planning
Cuts long-term repair costs
Whether you're running a surface mine or an underground operation, a proactive approach to equipment maintenance pays off — and it starts with a plan.
Key Elements of a Good Mining Maintenance Plan
1. Preventive Maintenance Scheduling
The backbone of any good maintenance plan is preventive maintenance (PM) — scheduled tasks performed to keep equipment running smoothly and prevent breakdowns before they occur.
Common PM tasks include:
Lubrication of moving parts
Fluid level checks and replacements
Hose and belt inspections
Filter replacements
Battery and electrical system testing
Wear part inspections (e.g., tires, undercarriage, teeth)
Maintenance intervals should be based on hour meter readings, manufacturer recommendations, and operating conditions. For example, machines working in wet or dusty mines may require more frequent inspections.
2. Condition-Based Monitoring (CBM)
A good mining maintenance strategy goes beyond the calendar. Condition-based monitoring uses real-time data from sensors to assess the health of a machine and trigger maintenance only when needed.
CBM tracks:
Oil quality and contamination
Vibration analysis
Temperature and pressure readings
Hydraulic system performance
Engine diagnostics
This approach helps avoid both over-maintenance and unexpected failures — improving equipment uptime while reducing unnecessary service costs.
3. Asset Inventory and Equipment Profiles
Each asset in your fleet should have a dedicated maintenance profile including:
Make, model, and serial number
Service history and repair logs
Component replacement schedule
Warranty status
Parts compatibility
Knowing the status of each machine in your operation helps prioritize tasks, predict wear-out dates, and order parts ahead of time.
Using fleet management software or a CMMS (Computerized Maintenance Management System) makes this process more accurate and efficient.
4. Qualified Personnel and Training
Your maintenance plan is only as effective as the people carrying it out. Having certified technicians and well-trained operators is essential.
Operators should be trained to:
Perform pre- and post-shift inspections
Identify abnormal sounds, leaks, or behavior
Report issues promptly with photos or notes
Technicians need to be familiar with:
Specific machine diagnostics
Safety procedures for repairs
Using diagnostic software and tools
Ongoing training ensures your team stays up-to-date with new technology, especially as more mining equipment incorporates remote diagnostics and telematics.
5. Effective Spare Parts Management
A good maintenance plan includes a spare parts inventory strategy. Delays in repairs often occur because the right part isn’t in stock when needed.
Best practices:
Maintain critical spares for high-failure components
Track usage trends to forecast needs
Partner with reliable OEM and aftermarket suppliers
Use labeling, barcoding, or RFID for faster tracking
Spare part availability is directly tied to how quickly a repair can be completed, minimizing downtime.
6. Emergency Repair Protocols
Even the best maintenance plans can’t prevent every issue. That’s why having a rapid response strategy for emergency repairs is crucial.
Include:
24/7 technician access or hotline
Mobile service trucks equipped for field repairs
Pre-authorized budgets for emergency purchases
Clear communication paths between operators and maintenance teams
Having a documented emergency maintenance workflow can shave hours off downtime when every minute counts.
7. Maintenance KPIs and Performance Tracking
To know if your plan is working, you need to track key performance indicators (KPIs).
Important mining maintenance KPIs include:
Mean time between failures (MTBF)
Mean time to repair (MTTR)
Equipment availability (%)
Planned maintenance vs. reactive maintenance ratio
Maintenance cost per operating hour
By reviewing performance data monthly or quarterly, you can identify areas for improvement and refine your plan.
8. Integration with Telematics and Remote Diagnostics
Modern mining fleets are increasingly using smart diagnostics systems that send real-time alerts about equipment performance, fault codes, and wear indicators.
Integrating platforms like:
Caterpillar Product Link
Komatsu KOMTRAX
Volvo CareTrack
...allows your team to receive alerts before issues become critical, remotely diagnose problems, and prepare service actions in advance — improving first-time fix rates and reducing technician travel time.
9. Safety and Compliance Procedures
All maintenance tasks should follow OSHA and MSHA safety standards, including lockout/tagout, confined space entry, and hot work procedures.
Make sure your maintenance plan addresses:
PPE requirements
Safety checklists for each machine
Documentation and compliance logs
Incident tracking and root cause analysis
A safe maintenance environment not only protects workers but also prevents costly violations or insurance issues.
Final Thoughts: Building a Plan That Works
A good mining maintenance plan is proactive, structured, and adaptable. It’s built around the specific needs of your equipment, your team’s capabilities, and your production goals. While no two mines are the same, every operation benefits from a plan that minimizes downtime, extends machine life, and creates a safer work environment.
By implementing preventive and condition-based maintenance, training your team, managing spare parts, and using performance data to drive decisions, you can stay ahead of costly breakdowns and maintain a more reliable, productive operation.