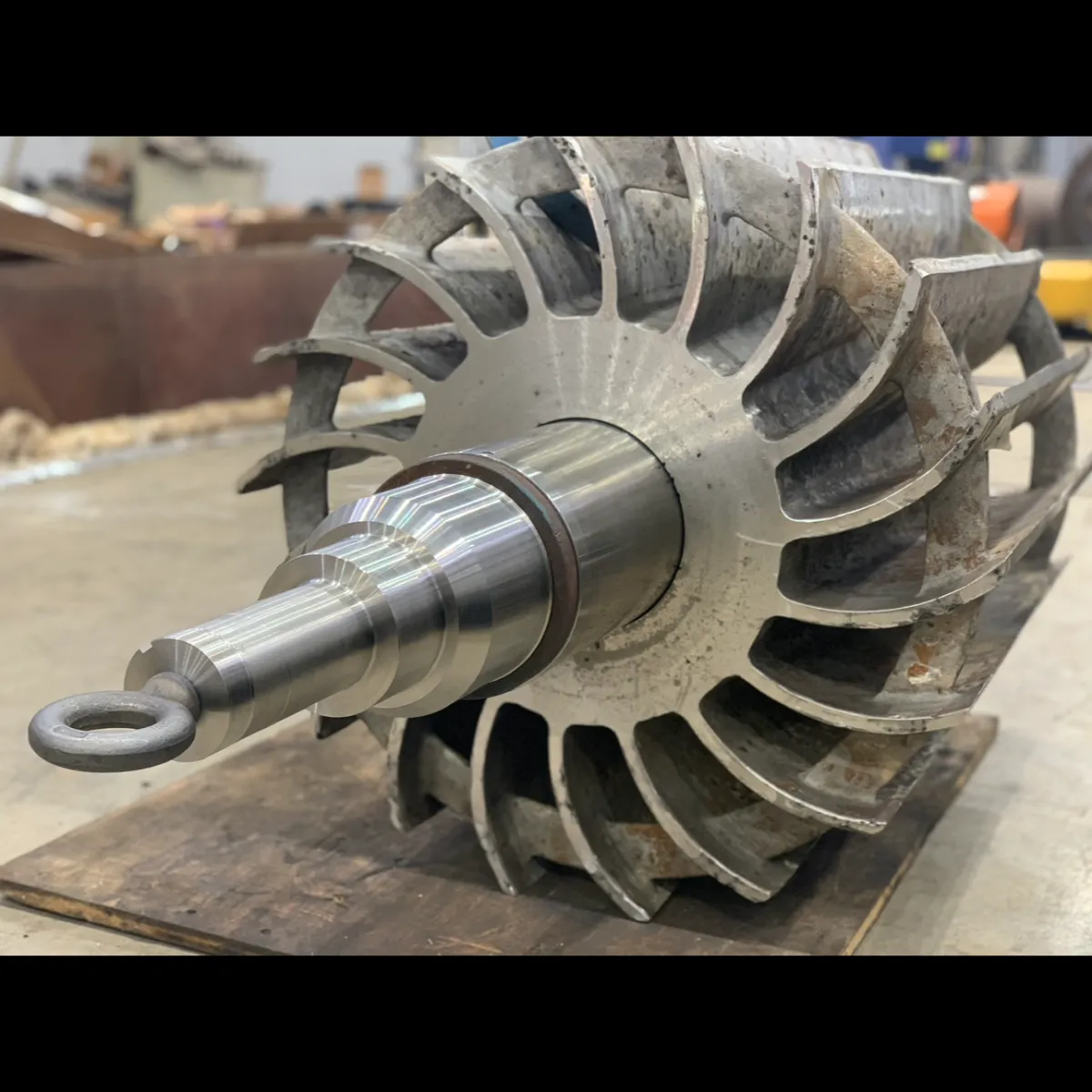
Welding Techniques Used in Equipment Restoration
Welding Techniques Used in Equipment Restoration
In industries like mining, construction, and agriculture, heavy equipment faces extreme wear and stress. Over time, components such as buckets, frames, blades, and arms suffer from cracks, corrosion, and fatigue. Replacing these parts can be costly and time-consuming — which is why many companies turn to equipment restoration through welding as a reliable, cost-effective solution.
Welding plays a crucial role in restoring structural integrity, extending equipment lifespan, and minimizing downtime. In this article, we’ll explore the most commonly used welding techniques in equipment restoration, their applications, and how to choose the right method for the job.
Why Welding Is Essential for Equipment Restoration
Heavy equipment operates in some of the harshest environments — from underground mines to rock quarries. Welding allows operators to:
Rebuild worn surfaces
Repair structural cracks
Reinforce weak joints
Attach wear-resistant materials
Restore OEM specs without full replacement
Instead of discarding damaged components, welding gives them a second life, saving money and reducing waste.
Common Welding Techniques in Equipment Repair and Restoration
1. Shielded Metal Arc Welding (SMAW / Stick Welding)
Best for: Outdoor repairs, thick materials, general-purpose restoration
Description: SMAW, often referred to as stick welding, is one of the oldest and most versatile welding methods. It uses a consumable electrode coated in flux, which forms a protective gas shield when melted.
Pros:
Excellent for dirty, rusty, or weathered surfaces
Portable and ideal for field repairs
Works well on thick carbon steel parts
Common Use Cases:
Repairing cracks in dozer blades
Rebuilding excavator bucket edges
Reinforcing frame structures in mobile equipment
2. Gas Metal Arc Welding (GMAW / MIG Welding)
Best for: Shop-based restoration, thinner materials, high-speed welds
Description: MIG welding uses a continuously fed wire electrode and a shielding gas to produce clean, consistent welds. It’s faster and easier to learn than other processes.
Pros:
High deposition rate (faster repairs)
Minimal spatter, clean welds
Great for repetitive restoration tasks
Common Use Cases:
Fabricating new brackets or support plates
Welding cracked guards or light attachments
Touch-ups on non-critical components
3. Flux-Cored Arc Welding (FCAW)
Best for: Heavy-duty welds, dirty materials, outdoor restoration
Description: FCAW is similar to MIG but uses a tubular wire filled with flux, eliminating the need for a separate shielding gas. It works well in windy or dusty environments.
Pros:
Great penetration for thick steel
Ideal for vertical or overhead welds
Performs well in the field
Common Use Cases:
Rebuilding wear plates on buckets
Hardfacing applications (wear resistance)
Repairing mobile mining equipment onsite
4. Gas Tungsten Arc Welding (GTAW / TIG Welding)
Best for: Precision repairs, aluminum, stainless steel
Description: TIG welding provides precise control using a non-consumable tungsten electrode and an external filler rod. It produces high-quality welds with excellent aesthetics.
Pros:
Extremely clean welds with minimal spatter
Strong welds on thin or delicate parts
Excellent control over weld puddle
Common Use Cases:
Restoring aluminum engine components
Small crack repairs on stainless or exotic metals
Custom fabrication of equipment parts
5. Oxy-Acetylene Welding and Cutting (OAW)
Best for: Preheating, cutting damaged sections, basic welds
Description: Oxy-acetylene involves combining oxygen and acetylene gas to generate a flame hot enough to melt metal. While not as common for structural welding, it’s useful for certain restoration jobs.
Pros:
Good for cutting and heating
Low-cost, portable equipment
Works without electricity
Common Use Cases:
Removing worn sections of frames
Preheating high-carbon steel to prevent cracking
Basic weld repairs on small equipment
Specialized Welding Applications in Equipment Restoration
1. Hardfacing
Hardfacing is the application of wear-resistant materials to surfaces exposed to friction or impact. It’s a crucial technique in mining and excavation.
Materials used: Chromium carbide, tungsten carbide, nickel-based alloys
Typical Parts: Bucket lips, cutting edges, crusher hammers, augers
Goal: Reduce wear, extend component life, and decrease downtime
2. Preheating and Post-Weld Heat Treatment (PWHT)
Certain high-carbon steels or cast materials require preheating to reduce the risk of cracking during welding. Post-weld heat treatment helps relieve stress and improve metal integrity.
Preheating: Raises the temperature of the metal before welding
PWHT: Slowly cools the weld area to avoid hardness and brittleness
Common Use Cases:
Dozer blades
Loader arms
Undercarriage frames
3. Crack Repair and Gouging
Before welding a crack, technicians often use arc gouging or grinding to remove the damaged metal and open up the joint. This ensures full penetration and a longer-lasting repair.
Tools used:
Carbon arc gouging torches
Plasma cutters
Angle grinders
Best Practices for Welding Equipment Restoration
Inspect the entire component — not just the visible damage
Choose the right filler material based on base metal
Control heat input to prevent warping or hardening
Test welds in high-stress areas using non-destructive testing (NDT)
Document all repairs for compliance and maintenance history
Training and Safety Considerations
Welding in industrial settings requires proper training, PPE, and procedures. Equipment repair welders should be certified in:
AWS D1.1 or D1.2 Structural Welding Code
Heavy equipment-specific procedures
Safety measures like fume extraction, arc flash protection, and fire safety
Always follow OSHA and MSHA regulations for hot work, confined spaces, and electrical safety.
Final Thoughts: Welding Brings Equipment Back to Life
Whether you're rebuilding a cracked loader arm, resurfacing a worn bucket edge, or fabricating a replacement bracket, welding is a powerful restoration tool. It allows businesses to maximize their equipment investment, minimize replacement costs, and keep operations moving.
Choosing the right welding technique depends on the material, thickness, environment, and intended outcome. With skilled technicians and a structured approach, welding extends the service life of even the hardest-working machines.