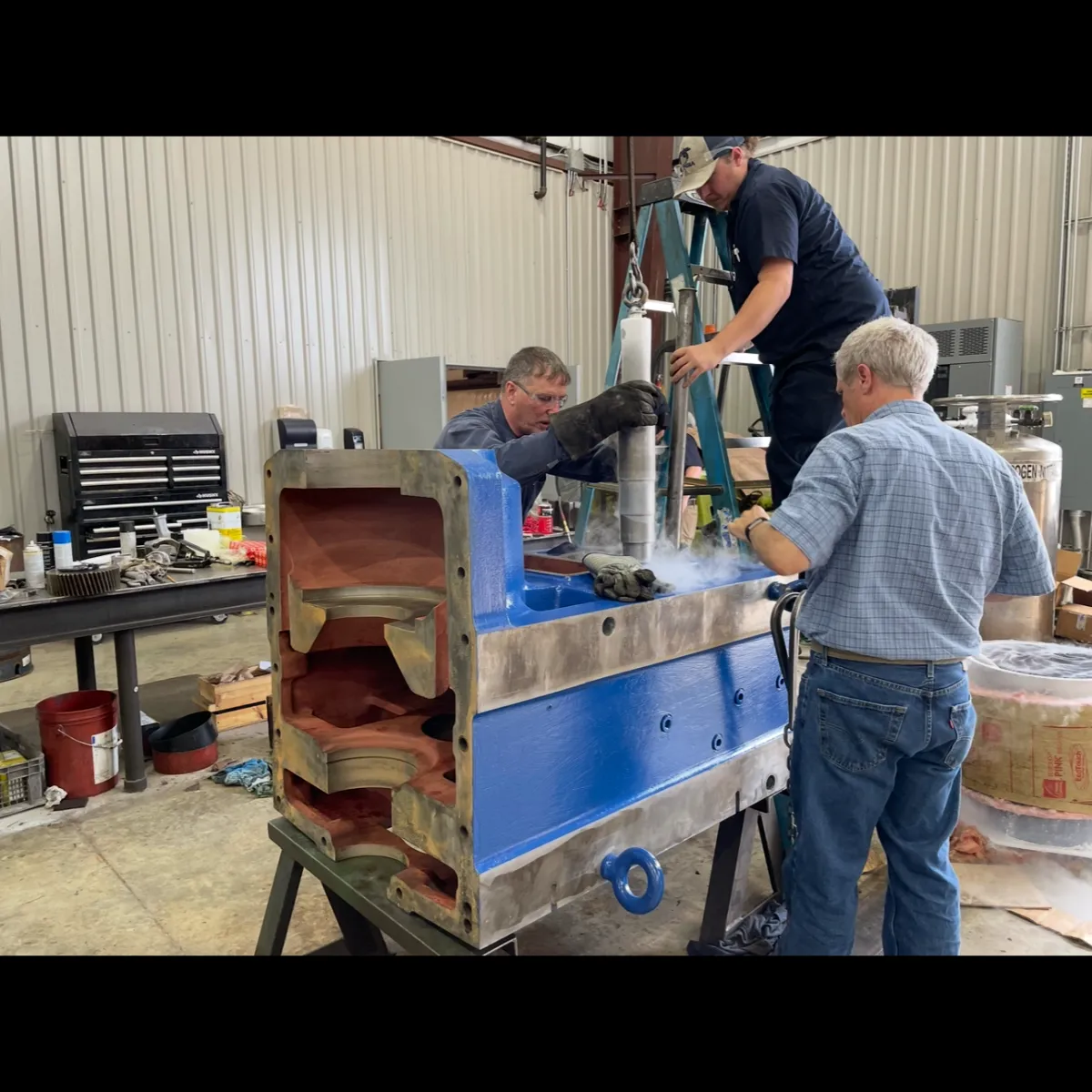
Top 3 Mistakes in Mining Equipment Maintenance
Top 3 Mistakes in Mining Equipment Maintenance
Mining operations run on precision, productivity, and performance. When equipment fails, production grinds to a halt — and every minute lost can cost thousands. That’s why mining equipment maintenance isn’t just a necessity — it’s a strategic function that directly impacts profitability, safety, and longevity.
Unfortunately, even experienced crews can fall into maintenance traps that lead to costly consequences. In this article, we’ll explore the top 3 most common mistakes in mining equipment maintenance, how they impact your operation, and most importantly, how to avoid them.
Mistake #1: Relying Solely on Reactive Maintenance
The Problem:
Many operations fall into the dangerous cycle of reactive maintenance — only fixing machines after they break down. While this may seem cost-effective in the short term, it’s often the most expensive and disruptive approach over time.
Breakdowns in mining equipment like crushers, haul trucks, drills, or conveyors can cause:
Sudden production stoppages
Emergency repair costs
Safety hazards for nearby crews
Equipment damage beyond the failed part
Delayed shipments and contract penalties
Real-World Example:
A mine waits for visible symptoms before inspecting a haul truck’s hydraulic system. The hose eventually ruptures under load, damaging surrounding components and leaking fluid into the work area — requiring environmental cleanup, a full system flush, and an unplanned 36-hour shutdown.
The Solution:
Adopt a proactive or predictive maintenance approach. Use:
Scheduled inspections based on equipment hours
Sensor-based monitoring systems (temperature, vibration, oil pressure)
CMMS software to track history and anticipate failure intervals
Oil sampling and fluid analysis to catch internal wear before it’s visible
Mining leaders are increasingly investing in predictive diagnostics and data-driven planning to minimize unplanned downtime and extend equipment life.
Mistake #2: Ignoring Daily Inspections and Greasing
The Problem:
Skipping daily walk-arounds, fluid checks, and greasing routines may save a few minutes upfront — but this shortcut often leads to avoidable equipment failure. Mining equipment operates under extreme stress and environmental exposure. Without regular attention, even the toughest machines will wear down fast.
Key issues caused by neglecting daily maintenance:
Unnoticed fluid leaks that damage engines or hydraulic systems
Loose bolts or pins that misalign assemblies
Dry joints and bushings leading to accelerated wear
Unreported cracks or stress fractures that spread under load
Real-World Example:
An operator skips the morning check on an excavator. The boom pin wasn’t greased for several days. Metal-on-metal friction eventually causes the bushing to seize and crack the pin housing — requiring welding, part replacement, and multi-day downtime.
The Solution:
Enforce a daily maintenance checklist, including:
Greasing pins and pivot points
Checking tire/tracks, lights, and electrical systems
Inspecting hoses, belts, filters, and seals
Verifying fluid levels and draining water separators
Logging and reporting any abnormalities
Using a mobile inspection app or paper log, with supervisor review, ensures accountability and consistency — even across large fleets or rotating crews.
Mistake #3: Using the Wrong Parts or Lubricants
The Problem:
In an effort to save money or reduce wait times, some crews use generic or incompatible parts and lubricants that don’t meet OEM standards. This often results in reduced performance, premature wear, or even catastrophic failure.
Common examples include:
Using low-grade hydraulic fluid in high-pressure systems
Installing aftermarket filters that don’t meet micron or flow specs
Using grease with the wrong NLGI grade or additives
Failing to match torque specs for replacement bolts or pins
Mixing incompatible fluids (e.g., coolant types)
These shortcuts may save a few dollars up front but can easily cause $10,000+ in collateral damage to pumps, valves, or drive systems.
Real-World Example:
A dozer’s transmission is filled with a non-OEM fluid during a field service. After 50 hours of use, the clutch packs begin slipping due to improper friction characteristics. The result? A full teardown and $30,000 in lost productivity and repairs.
The Solution:
Always follow manufacturer specifications for:
Fluids and filters
Seals, gaskets, and torque specs
Lubricants and grease types
Software and electronic components
Keep a digital or printed equipment manual on hand, and train technicians to verify part compatibility. Better yet, maintain a stocked inventory of critical OEM parts and approved consumables to reduce repair delays and avoid “patch jobs.”
Bonus Tip: Train Your Operators
Even the best maintenance strategy can fall apart without trained equipment operators. Operators are the first line of defense against costly breakdowns — but only if they’re trained to:
Detect warning signs (e.g., odd noises, performance drops, smoke, etc.)
Report issues immediately
Operate within recommended load and speed limits
Avoid abusive practices like hard braking, overloading, or dry starts
A well-trained operator will spot minor issues early, report them, and help prevent major failures before they happen.
Final Thoughts: Avoiding the Big Three
Maintenance mistakes in mining equipment aren’t just costly — they’re avoidable. By avoiding these top three pitfalls:
Reactive-only repairs
Skipping daily inspections and greasing
Using improper parts or lubricants
...you can greatly reduce downtime, extend equipment life, and boost site-wide safety and productivity.
Don’t leave maintenance to chance. Create a standardized system, use technology to stay on top of tasks, and invest in the tools, parts, and training your team needs to succeed.