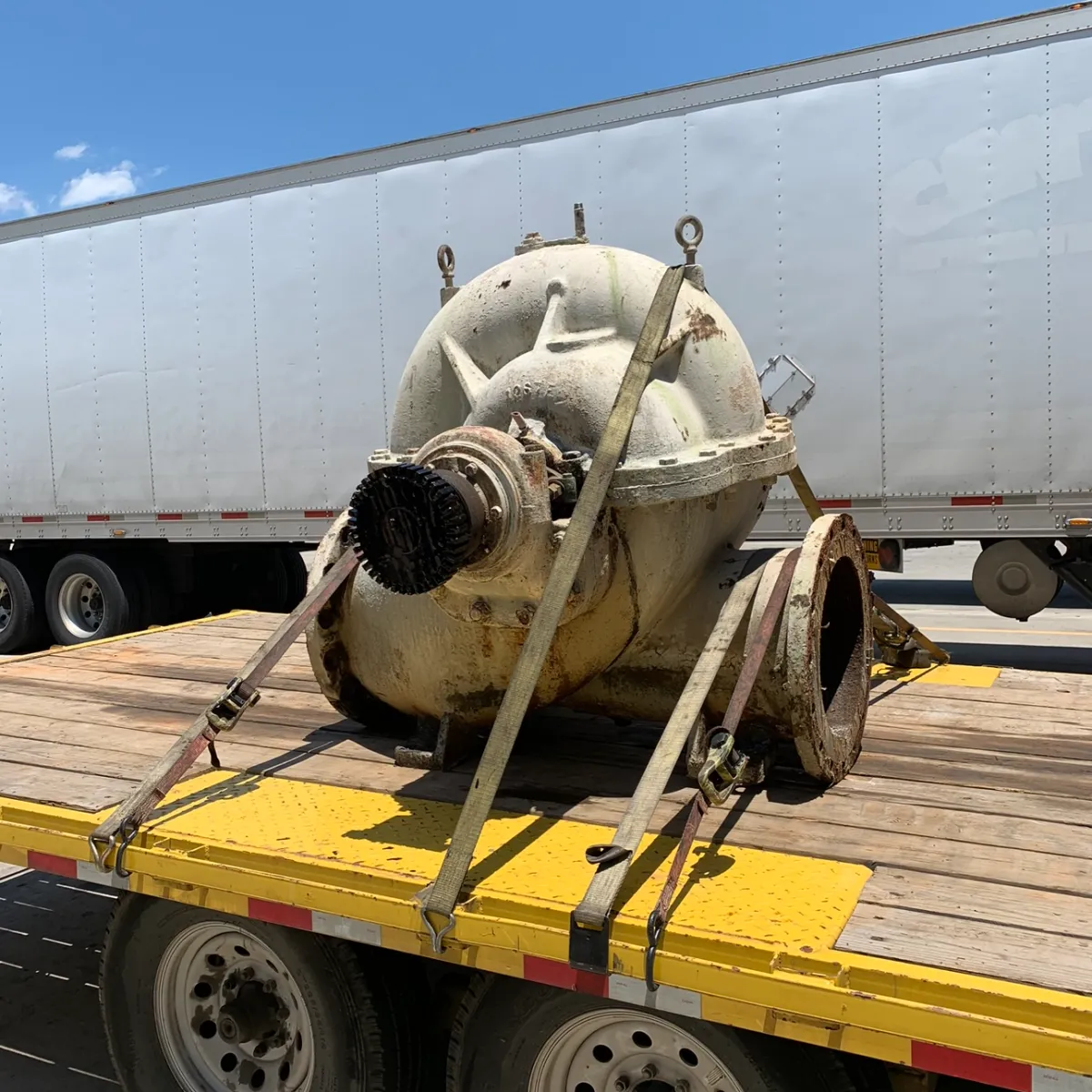
The Future of Smart Diagnostics in Mining Equipment
The Future of Smart Diagnostics in Mining Equipment
The mining industry is undergoing a rapid transformation, driven by a combination of automation, sustainability, and real-time intelligence. One of the most promising innovations is smart diagnostics in mining equipment — an emerging field that’s reshaping how operators detect problems, prevent failures, and extend machine lifespans.
As mining companies face increasing pressure to reduce downtime and maximize asset utilization, smart diagnostics are no longer a luxury — they’re becoming essential. This article explores the future of these systems and what it means for operators, technicians, and the broader mining ecosystem.
What Are Smart Diagnostics in Mining?
Smart diagnostics refer to embedded systems in mining machinery that use sensors, software, and data analytics to monitor equipment performance in real time. These systems automatically detect anomalies, generate fault codes, and even recommend repairs before a technician arrives.
They go far beyond traditional diagnostics — offering machine learning-powered predictions, condition-based monitoring, and remote diagnostics that improve both safety and productivity.
Key features include:
Real-time sensor data (temperature, pressure, vibration, etc.)
Predictive maintenance alerts
Integration with fleet management software
Automated reporting and log tracking
Remote access capabilities for technicians
Why the Industry Is Shifting Toward Smart Repair Tech
Mining operations often run 24/7 in remote, harsh environments where unexpected equipment failure can cost thousands per hour. Traditional scheduled maintenance is helpful, but it doesn't always prevent critical issues — especially with high-hour equipment.
Smart diagnostics enable condition-based maintenance, which means repairs are made based on actual equipment needs rather than fixed time intervals. This reduces unnecessary downtime and helps avoid catastrophic failures.
According to a report by Deloitte, mining companies implementing predictive diagnostics have reduced unplanned downtime by as much as 20–30%.
How Smart Diagnostics Work in Mining Equipment
Modern mining equipment, from haul trucks and dozers to crushers and loaders, is now equipped with dozens of integrated sensors. These sensors monitor:
Engine temperature and fuel efficiency
Hydraulic system pressure and fluid levels
Component wear and tear
Gearbox vibration and transmission health
Brake systems and tire conditions
Electrical system voltages and current flow
The data collected is sent to an onboard computer or remote diagnostic center, where it’s processed using AI algorithms. These tools can detect minute changes in performance patterns — sometimes before any symptoms are visible to human operators.
When irregularities are detected, the system may:
Send an alert to a technician’s tablet
Log a fault code for later reference
Automatically request a mobile repair technician
Provide suggestions on which part is likely failing
Benefits of Smart Diagnostic Tools in Mining Equipment
There are multiple advantages to using smart diagnostic systems in the mining industry:
1. Increased Uptime:
By catching issues early, you avoid large-scale breakdowns. Machines spend more time working and less time being inspected or repaired manually.
2. Cost Savings on Repairs:
Knowing exactly what’s wrong allows technicians to bring the right tools and parts the first time, reducing labor costs and part replacements.
3. Improved Technician Efficiency:
Technicians can rely on diagnostic data rather than time-consuming trial-and-error inspections, streamlining the repair process.
4. Real-Time Fleet Visibility:
Fleet managers can monitor all assets from a central dashboard, tracking machine health, usage trends, and upcoming service needs.
5. Enhanced Safety:
Machines experiencing dangerous conditions — like overheating, pressure surges, or electrical shorts — can be shut down automatically before injury occurs.
Smart Diagnostics and Predictive Maintenance: A Powerful Duo
Smart diagnostics alone provide incredible visibility. But when paired with predictive maintenance software, the impact is multiplied.
Predictive systems use historical data to anticipate failures before they happen. For example, if a haul truck’s brake pressure typically drops before a cylinder leak, the software can flag this pattern early. Instead of waiting for the leak to occur, a technician is dispatched preemptively to swap the cylinder, avoiding emergency downtime.
Systems like Komatsu’s KOMTRAX, CAT’s Product Link, and Epiroc’s Certiq are already leading the way in this technology. These platforms are paving the future of AI-powered mining repairs.
The Role of Remote Diagnostics and Telematics
Smart diagnostics are increasingly paired with telematics — the use of wireless communication to send diagnostic information to a central hub.
In the near future, expect:
Remote troubleshooting sessions, where offsite technicians guide on-site teams step-by-step.
Mobile repair vans equipped with diagnostic tablets and part inventories based on pre-diagnosed faults.
Cloud-connected mining fleets, where repair data is shared across regions to learn from global machine performance trends.
This reduces the need for sending technicians blindly into the field — saving both time and fuel, while dramatically improving first-time fix rates.
Challenges and Considerations
While the benefits are clear, the transition to smart diagnostics isn’t without obstacles:
Cost of Implementation: Retrofitting older machines or investing in sensor-rich equipment can be costly upfront.
Data Overload: Not all teams are equipped to process and act on large volumes of performance data.
Training Needs: Both operators and technicians must be trained to interpret fault codes and trust system alerts.
Security: Remote systems must be secured against cyber threats, especially with the rise of connected infrastructure.
Despite these concerns, the industry trend is clear — more mining companies are shifting toward smarter systems to stay competitive.
Conclusion: The Future Is Intelligent, Predictive, and Preventive
Smart diagnostics in mining equipment are no longer a futuristic vision — they are actively redefining how we think about mining equipment repairs and operational uptime. As machines become more intelligent and interconnected, the role of the technician is also evolving. Tomorrow’s mining repair tech will need to blend mechanical expertise with digital literacy, interpreting data as easily as they wield wrenches.
Companies that embrace these tools now will be better positioned for productivity, safety, and long-term success.