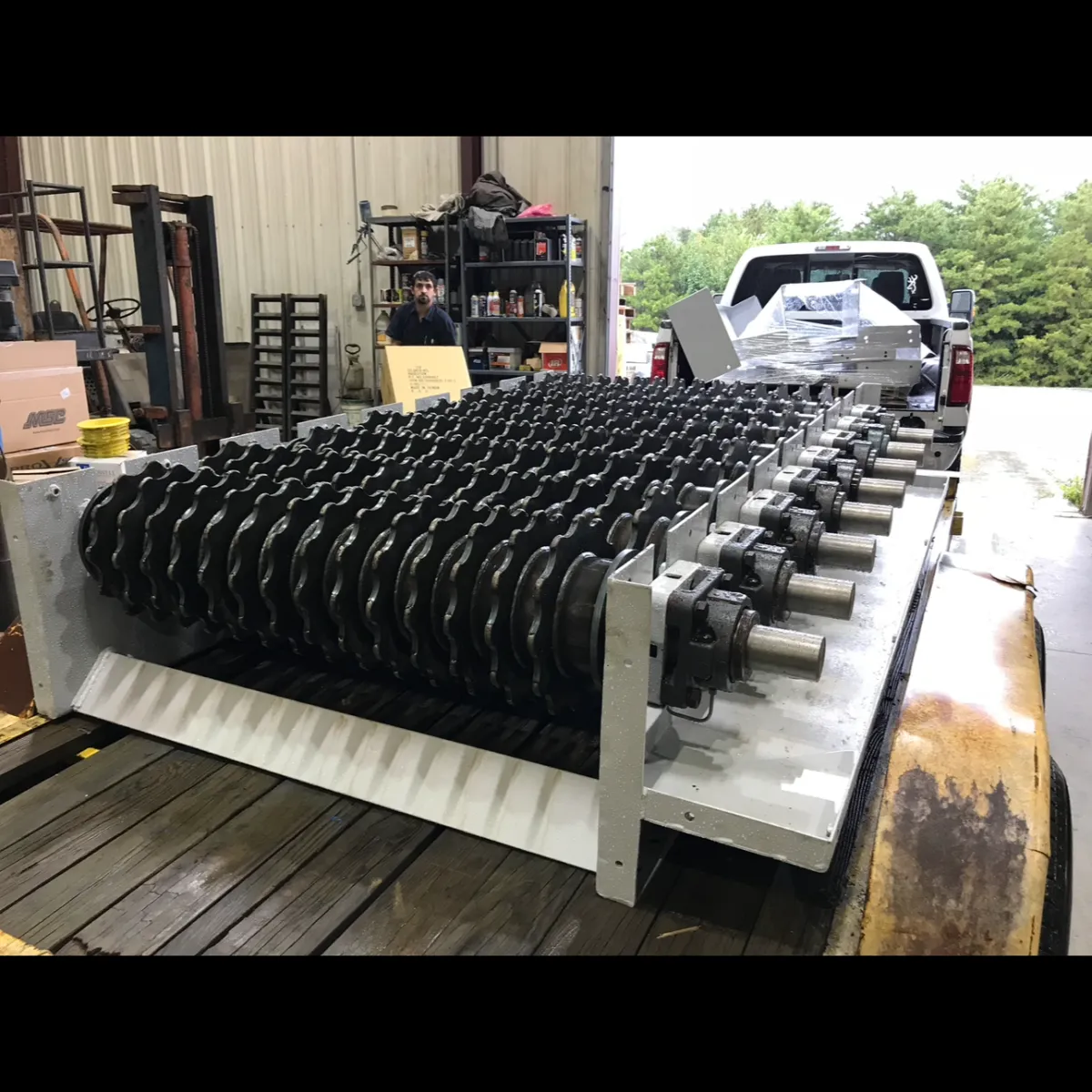
Latest Trends in Equipment Longevity
Latest Trends in Equipment Longevity
As industries like mining, construction, agriculture, and manufacturing face increasing pressure to maximize uptime and reduce replacement costs, the focus on equipment longevity has never been greater. In 2025 and beyond, organizations are leveraging cutting-edge technologies and smarter maintenance practices to extend the operational life of heavy machinery and infrastructure.
This article explores the latest trends in equipment longevity, from AI-driven maintenance and digital twins to sustainability initiatives that reduce environmental impact while improving machine life.
1. Predictive Maintenance Powered by AI
One of the most transformative trends in equipment longevity is the use of predictive maintenance. Rather than relying on scheduled servicing or reacting to breakdowns, companies now use artificial intelligence and machine learning to anticipate failures before they happen.
How it works:
IoT sensors collect real-time data from equipment (temperature, pressure, vibration, etc.)
AI algorithms analyze the data for anomalies
Maintenance is triggered only when early signs of wear or failure are detected
Benefits:
Extends asset life
Reduces unplanned downtime
Minimizes labor and parts costs
Systems like Caterpillar’s Product Link™, Komatsu KOMTRAX™, and Volvo’s ActiveCare™ are already setting the industry standard in predictive diagnostics.
2. Digital Twins and Virtual Equipment Modeling
A digital twin is a real-time digital replica of a physical asset. It mirrors the behavior, wear, and condition of a machine throughout its life, using data from sensors, operating logs, and service history.
Use cases:
Simulating different operating conditions
Forecasting failure modes
Testing upgrades or maintenance strategies virtually
Digital twins are increasingly being used in heavy equipment lifecycle management, enabling smarter decisions on repairs, refurbishments, or replacement timing.
3. Real-Time Monitoring and Telematics
Connected equipment is the norm, not the exception. Telematics systems provide operators and fleet managers with live insights into:
Fuel usage
Idle time
Engine hours
Maintenance alerts
Fault codes
With this data, companies can address small issues before they become large, costly repairs. It also ensures equipment is being operated within optimal parameters, which contributes significantly to longer service life.
4. 3D Printing and Additive Manufacturing for Spare Parts
Delays in obtaining OEM parts can lead to excessive equipment downtime. To combat this, many operators are embracing additive manufacturing (aka 3D printing) to produce:
Replacement gears
Brackets and mounts
Custom bushings and seals
This trend reduces the lead time on part delivery and keeps older equipment — where spare parts are no longer manufactured — in operation longer.
5. Sustainability and Rebuild Programs
Environmental sustainability is becoming a major driver behind equipment longevity. Instead of scrapping worn-out machines, companies are:
Rebuilding engines, transmissions, and undercarriages
Refurbishing body frames
Reusing major components
OEMs like Caterpillar and Komatsu now offer certified rebuild programs that restore used machines to like-new condition, extending lifespan while reducing environmental waste.
6. Advanced Lubrication and Fluid Analysis
Lubrication technology has advanced significantly. Synthetic oils, biodegradable lubricants, and smart grease solutions now offer:
Longer service intervals
Improved thermal stability
Resistance to moisture and contamination
In addition, fluid analysis is a growing trend. Regular lab testing of oil and coolant helps predict component wear, catch early signs of contamination, and optimize service schedules — all of which boost equipment life.
7. Automated Maintenance Scheduling Through CMMS
A Computerized Maintenance Management System (CMMS) automates service tasks and ensures nothing falls through the cracks. Key features include:
Work order creation
Parts inventory tracking
Scheduled maintenance alerts
Technician checklists
Integrating CMMS with telematics and predictive tools creates a fully connected equipment maintenance ecosystem, ensuring the machine is always serviced on time and according to usage patterns.
8. Remote Diagnostics and Over-the-Air Updates
Manufacturers are integrating remote diagnostics tools that allow support teams to monitor and even fix issues from afar. In many cases, software updates can be pushed wirelessly, resolving performance bugs or unlocking improved settings.
This reduces the need for service visits, lowers repair time, and ensures machines always operate with the most up-to-date technology — supporting long-term performance and reliability.
9. Operator Behavior Monitoring and Training
The way equipment is operated greatly impacts its lifespan. Harsh starts, excessive idle time, or improper load handling all accelerate wear. Now, telematics systems are used to:
Monitor operator behavior
Provide training feedback
Identify misuse or unsafe practices
With better-trained operators and clear data insights, equipment suffers fewer operational stresses — directly contributing to longevity.
10. Equipment as a Service (EaaS) and Lifecycle Management
The Equipment as a Service (EaaS) model is changing how businesses view ownership. Instead of purchasing equipment outright, companies lease it from OEMs or third parties who manage all maintenance and performance optimization.
These providers are incentivized to maximize equipment uptime and extend service life, using predictive analytics, remote diagnostics, and performance-based contracts.
11. Sustainable Design and Build Innovations
Manufacturers are incorporating modular components, corrosion-resistant materials, and smart design features that reduce failure points and make maintenance easier.
Examples include:
Bolt-on wear components for faster replacement
Reinforced bushings and pivot points
Coated pins to resist rust
All of these innovations contribute to fewer breakdowns and longer operational life.
Final Thoughts: Longevity Is the New Standard
Gone are the days when heavy equipment was treated as disposable. With rising costs, tighter regulations, and growing environmental awareness, extending equipment life is now a strategic priority.
From predictive analytics and digital twins to 3D printing and CMMS platforms, today’s trends focus on proactive care, smarter decisions, and sustainable practices. Businesses that adopt these innovations aren’t just saving money — they’re building smarter, stronger fleets for the future.