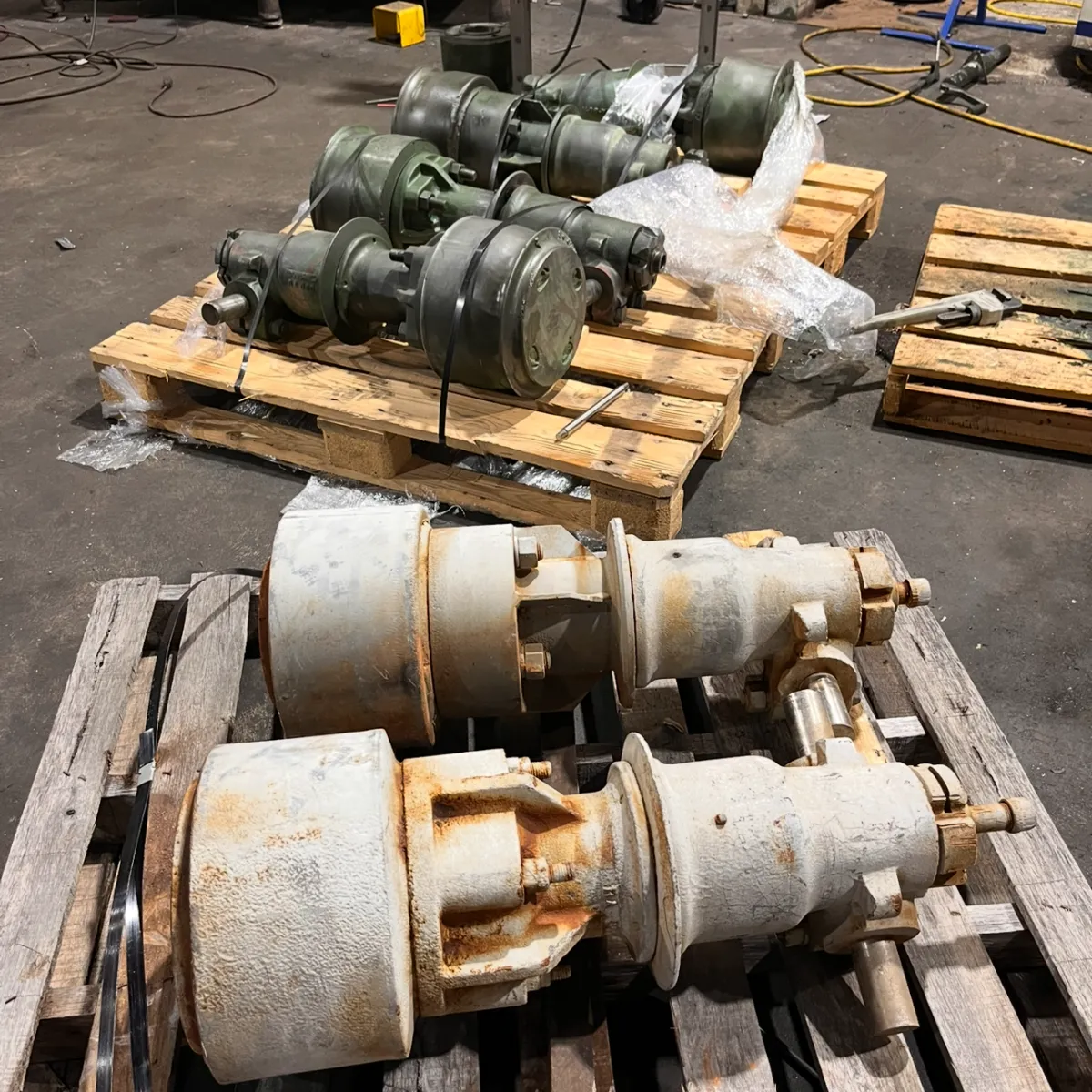
Importance of Clean Fuel Systems in Large Equipment
Importance of Clean Fuel Systems in Large Equipment
In the world of heavy-duty machinery — whether it’s mining trucks, bulldozers, agricultural equipment, or construction vehicles — fuel system integrity is critical. Engines are the heart of large equipment, and clean fuel systems are essential for keeping those engines running smoothly, efficiently, and without interruption.
Contaminated fuel, clogged filters, or damaged injectors can bring an entire operation to a halt, resulting in expensive downtime, safety risks, and costly repairs. This article explores the importance of clean fuel systems in large equipment, the consequences of fuel contamination, and best practices to keep systems running at peak performance.
What Is a Fuel System and Why Does Cleanliness Matter?
A fuel system delivers diesel or gasoline from the tank to the engine at the correct pressure and flow rate. Key components include:
Fuel tank
Fuel lines
Filters
Pumps
Injectors
Fuel rail (in some systems)
These systems are built with high-precision components. Even tiny particles or water droplets can cause significant damage or performance issues. That’s why cleanliness is crucial — it ensures reliable combustion, prevents engine wear, and supports optimal fuel efficiency.
What Happens When Fuel Systems Aren’t Clean?
1. Clogged Fuel Filters
Fuel filters are your first line of defense against contaminants. When they get overwhelmed, they restrict flow and starve the engine of fuel, causing:
Hard starts or failure to start
Power loss under load
Poor acceleration
Inconsistent idle or stalling
2. Injector Damage
Fuel injectors are finely tuned to atomize fuel in precise amounts. Dirt, debris, or water can damage the nozzles, resulting in:
Uneven spray patterns
Incomplete combustion
Smoke emissions
Increased fuel consumption
Engine knocking or misfires
3. Fuel Pump Wear
Contaminants act like sandpaper inside the fuel pump, leading to premature wear or failure. A failing fuel pump can cause sudden shutdowns, especially under load.
4. Water Contamination and Microbial Growth
Water in fuel tanks promotes bacteria and fungus, which form sludge and corrosion inside tanks, lines, and filters. This microbial contamination can clog systems and eat away at metal components.
5. Injector Overheating in Modern Engines
High-pressure common rail systems operate at extreme temperatures and tolerances. Contamination causes injector overheating, resulting in reduced performance and long-term engine damage.
Why Clean Fuel Systems Are Crucial in Large Equipment
1. Maximizes Engine Performance
Clean fuel systems deliver fuel precisely, allowing the engine to operate at peak efficiency. This means more power output, smoother operation, and better throttle response — essential for demanding tasks like excavation, hauling, or land clearing.
2. Reduces Fuel Consumption
Contaminants can disrupt combustion and lead to fuel wastage. A clean system ensures better combustion, reducing fuel burn and saving costs — especially important with large equipment consuming hundreds of gallons per week.
3. Prevents Costly Downtime
Breakdowns due to clogged filters or injector failures often require field service or towing to a shop. Clean fuel systems reduce unscheduled maintenance, keeping machines running and jobs on schedule.
4. Extends Engine Life
Clean fuel minimizes internal wear in pumps, injectors, and combustion chambers. Over time, this translates to longer engine life, fewer rebuilds, and better resale value for your fleet.
5. Supports Emissions Compliance
Modern diesel engines are equipped with advanced emission systems (like DPF and SCR). Contaminated fuel can increase soot output and clog after-treatment systems — leading to compliance violations and downtime for forced regeneration or DPF cleaning.
Signs Your Fuel System Might Be Dirty
Difficulty starting or frequent stalling
Black or white smoke from exhaust
Noticeable power loss during operation
Excessive fuel consumption
Loud knocking or pinging sounds
Dirty or blackened fuel filter during inspection
Visible water or sludge in the tank or water separator
If you notice any of these, it’s time to inspect, clean, or service the fuel system.
Best Practices for Maintaining Clean Fuel Systems
1. Use High-Quality Fuel
Start with the basics. Always use fuel from trusted suppliers, and make sure it meets ASTM D975 diesel fuel standards. Poor-quality fuel increases the risk of contamination from the start.
2. Store Fuel Properly
If you store fuel onsite:
Use filtered dispensing nozzles
Keep tanks sealed and protected from rain or condensation
Use water absorbers or fuel stabilizers
Inspect tanks regularly for sediment and microbial growth
3. Change Filters on Schedule
Follow manufacturer guidelines for primary and secondary filter replacements. Consider more frequent changes if operating in dusty, humid, or contaminated environments.
4. Drain Water Separators
Many diesel systems include fuel/water separators. These should be checked and drained daily or as recommended by the OEM — especially in wet conditions.
5. Use Fuel Additives (When Approved)
Some additives help clean injectors, remove water, or boost cetane levels. Only use those approved for your engine type and consult your manufacturer for compatibility.
6. Flush the System if Contaminated
In cases of severe fuel contamination, you may need to:
Remove and clean the tank
Replace all filters
Flush fuel lines
Clean or replace injectors
Inspect and test fuel pumps
It’s better to act early than risk engine damage or failure.
Technologies That Help Maintain Clean Fuel Systems
Fuel Polishing Systems: Clean stored fuel by removing water, sludge, and contaminants
Inline Fuel Conditioners: Protect against microbe growth and particulate damage
Telematics Alerts: Many modern systems flag early fuel pressure drops or injector errors for quick diagnosis
CMMS Maintenance Logs: Helps track fuel filter changes, contamination events, and maintenance intervals
Final Thoughts: Clean Fuel, Strong Machines
Fuel is the lifeblood of large equipment. A clean fuel system ensures that every drop delivers power efficiently, safely, and without compromise. When fuel systems are ignored, equipment performance suffers, maintenance costs rise, and downtime becomes inevitable.
By following best practices, monitoring for early signs, and investing in proper fuel storage and maintenance, your operation can protect its most valuable assets: your engines, your uptime, and your bottom line.