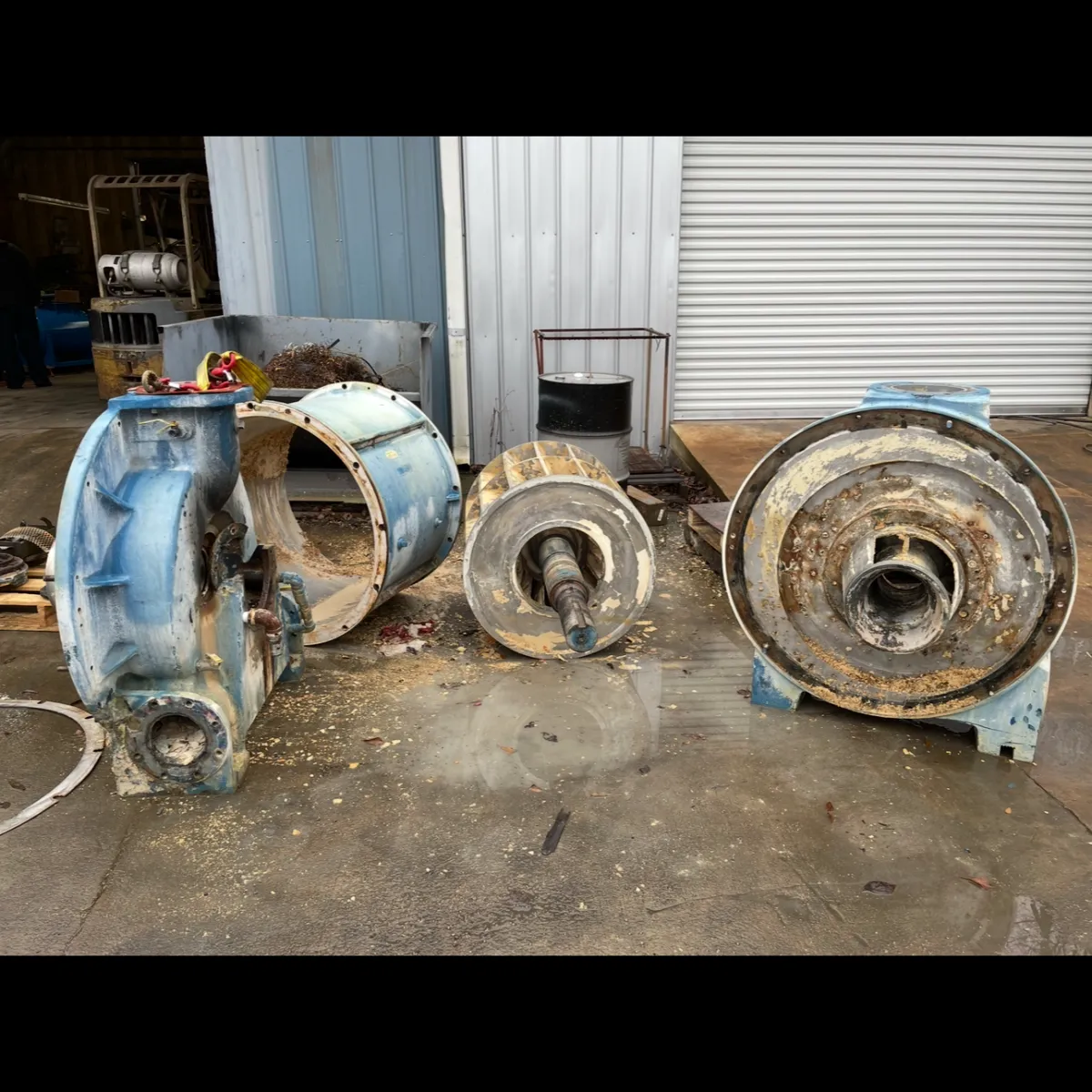
How Wear and Tear Impacts Bucket Efficiency
How Wear and Tear Impacts Bucket Efficiency in Mining and Heavy Equipment
In industries like mining, construction, and excavation, the bucket is one of the most frequently used — and most abused — attachments. From digging and lifting to loading and breaking through rock or clay, buckets take on some of the toughest tasks on site. Over time, this constant usage leads to wear and tear, which directly affects bucket efficiency, performance, fuel economy, and even machine lifespan.
Understanding how wear develops and how it impacts your operations is essential to maximizing productivity and minimizing downtime. This article breaks down the key ways wear and tear reduce bucket efficiency, and what you can do to extend the life of your equipment.
Why Bucket Efficiency Matters
The bucket is a frontline tool. Its condition has a direct influence on:
Digging speed
Cycle times
Machine strain and fuel use
Material load per scoop
Safety of operations
When your bucket isn’t functioning at peak efficiency, you’re losing productivity with every pass — especially in operations that move thousands of yards of material daily.
For companies in mining, quarrying, or site prep industries, these losses add up fast. That’s why understanding wear patterns and monitoring component health is critical to avoiding costly performance dips.
Common Types of Wear in Buckets
Buckets used in mining and heavy construction are exposed to abrasive materials, high-impact forces, and constant friction. The most common wear areas include:
1. Cutting Edge Wear
The cutting edge is responsible for slicing through material — whether it's soft soil or hard rock. Over time, this edge dulls, which increases resistance during digging and reduces cutting efficiency. Dull edges also increase stress on the loader arm and hydraulic system.
2. Bucket Teeth Degradation
Teeth are the first point of contact with the ground. They wear quickly and unevenly if not monitored. Broken or uneven teeth reduce digging speed and lead to imbalanced loading, which can damage other components.
3. Side Wall and Corner Wear
Side plates and corners are subject to scraping and impact from rocks or trench walls. If left unchecked, wear can weaken structural integrity and lead to cracks or deformation.
4. Heel and Floor Wear
The bottom of the bucket — particularly the heel area — often drags across abrasive surfaces. This leads to thinning steel, loss of structural support, and eventually holes in the bucket base.
5. Adapter and Shank Damage
If worn teeth aren't replaced, the adapter or shank system can become damaged. This leads to improper alignment and poor tooth retention, further reducing efficiency.
The Impact of Wear on Performance and Costs
Reduced Material Load Per Cycle
As the bucket degrades, it loses volume and shape. A worn cutting edge or missing teeth results in less material per scoop, directly affecting your per-cycle productivity.
Increased Fuel Consumption
When the bucket isn't cutting or filling efficiently, the operator must exert more force, take more passes, or reposition the machine multiple times. This leads to longer cycle times and higher fuel burn.
Accelerated Machine Wear
Buckets that don’t cut cleanly or load smoothly place more strain on the boom, linkage, hydraulics, and even undercarriage. What starts as minor bucket wear can eventually shorten the lifespan of your entire machine.
Operator Fatigue and Inefficiency
An inefficient bucket causes more resistance and bounce, forcing the operator to compensate with extra movements and extended working hours — increasing fatigue and the likelihood of operational errors.
Unexpected Downtime
When wear is left unaddressed, it can lead to sudden failures, such as broken shanks, cracked side walls, or detached components — halting operations entirely.
Warning Signs of Decreased Bucket Efficiency
Visible cracks or worn-through metal on the heel or bottom
Dull or missing teeth
Irregular or uneven tooth pattern
Shiny, thinned-out metal on wear surfaces
Poor bucket fill or difficulty penetrating material
Hydraulic strain or audible stress during digging
Bucket bouncing or erratic movement under load
How to Extend Bucket Life and Maintain Efficiency
1. Perform Routine Inspections
Daily or shift-based inspections should include a visual check of the teeth, cutting edge, sidewalls, and attachment points. Use a flashlight to check for stress cracks or hairline fractures.
2. Replace Teeth Early
Waiting too long to replace worn teeth leads to damaged shanks and adapters. Teeth are relatively inexpensive compared to the repair costs of mounting hardware or entire buckets.
3. Use Wear Protection Products
Install wear plates, shrouds, heel guards, and side cutters to protect high-contact areas. These components are designed to absorb damage before the bucket itself wears out.
4. Match the Bucket to the Job
Using the wrong bucket type or size for the material can lead to excessive wear. For example, using a general-purpose bucket in high-abrasion environments like granite quarries will wear out components rapidly.
5. Implement Rotating Maintenance Schedules
If your operation uses multiple machines, rotate buckets and attachments between light-duty and heavy-duty tasks. This helps distribute wear evenly across your fleet.
6. Leverage Smart Telematics
Modern equipment with telematics systems (such as Caterpillar Product Link or Komatsu KOMTRAX) can monitor digging efficiency, hydraulic strain, and cycle times to help predict when wear is affecting performance.
When to Repair vs. Replace a Bucket
In many cases, timely repairs — like hardfacing, welds, or plate replacements — can extend the life of a bucket significantly. However, if:
There are multiple structural cracks
The floor is worn through
The mounting frame is compromised
Adapter systems are heavily corroded or misshapen
…it may be more cost-effective to replace the bucket entirely. Always consult a qualified repair technician who can perform a bucket wear assessment.
Final Thoughts: Keep Your Buckets in Top Shape
Your bucket is more than just a steel scoop — it’s the critical link between your machine and the work it performs. Even small amounts of wear can drastically reduce bucket efficiency, raise costs, and increase the burden on your entire fleet.
Staying proactive with inspections, wear part replacement, and preventive maintenance is key to staying productive and profitable. For operations in mining, construction, or aggregates — especially those in high-wear environments like Georgia — partnering with a trusted equipment repair service ensures you're never caught off guard.