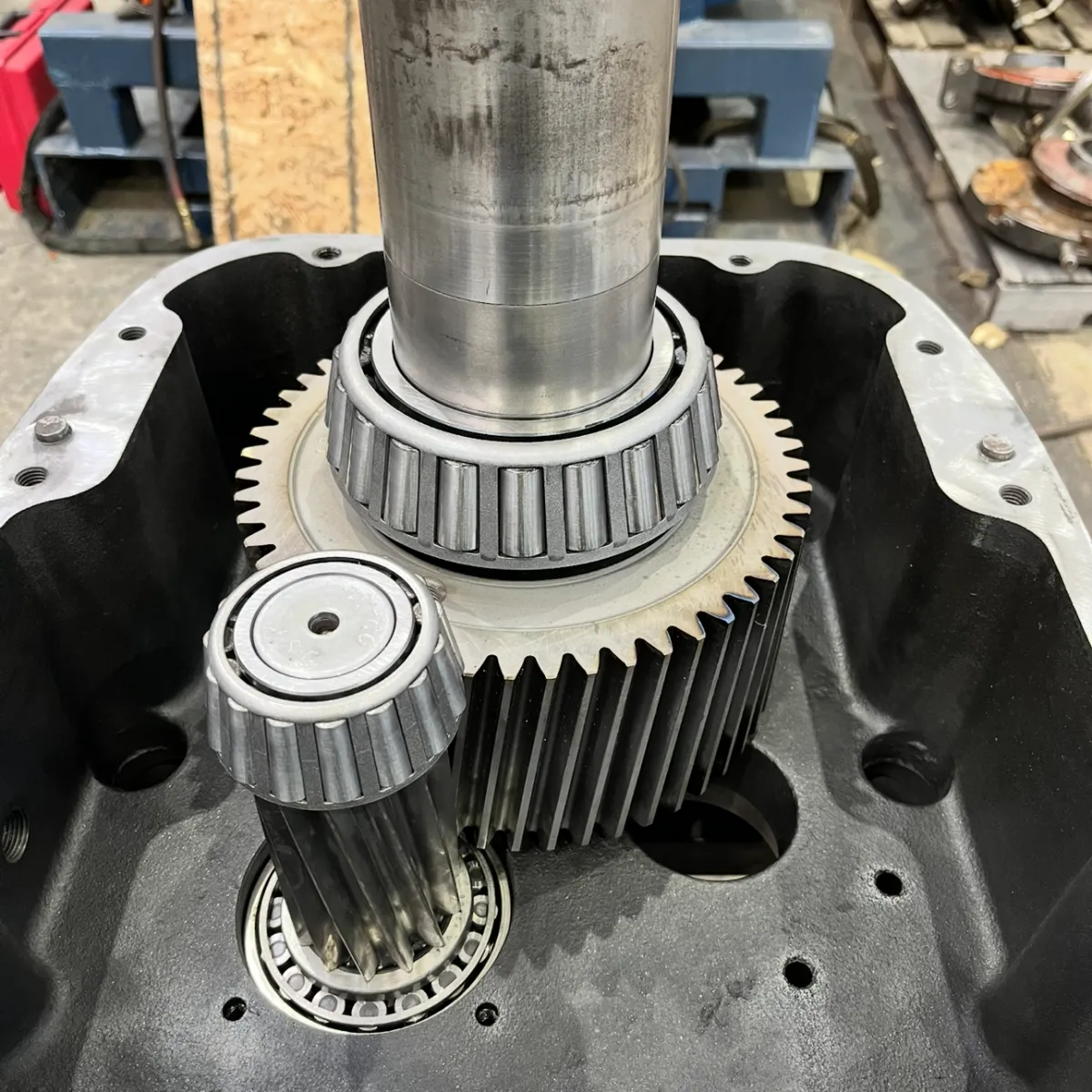
How We Prepare Equipment for Harsh Climates
How We Prepare Equipment for Harsh Climates
Heavy-duty equipment isn’t just expected to perform — it’s expected to perform everywhere, from scorching desert sites to sub-zero arctic zones. In mining, construction, forestry, and oil & gas, operations often take place in harsh climatesthat push both machines and maintenance crews to the limit.
To maximize uptime and avoid costly breakdowns, it’s essential to prepare equipment for extreme environments. In this guide, we’ll break down how we winterize, heat-proof, and fortify machines for the world’s toughest working conditions — from sandstorms to blizzards.
Why Equipment Needs Special Prep for Harsh Climates
Whether it's extreme heat, cold, dust, salt, or moisture, environmental stressors can:
Accelerate component wear
Affect fluid performance
Cause electrical and fuel system failures
Lead to dangerous operating conditions
By making proactive adjustments, we prevent damage, improve safety, and extend equipment life in places where even a minor failure can mean thousands in downtime or jeopardize worker safety.
Preparing for Cold Weather Conditions
1. Cold-Weather Fluids and Lubricants
Regular engine oils and hydraulic fluids thicken in low temperatures, leading to poor circulation and sluggish response. We switch to:
Low-viscosity oils rated for sub-zero temps
Cold-weather hydraulic fluid to prevent pump cavitation
Diesel fuel additives to prevent gelling and improve ignition
2. Battery and Electrical Prep
Cold weather reduces battery capacity. To ensure reliability, we:
Install high CCA (cold cranking amps) batteries
Test alternators and starters before winter
Use battery warmers or blankets in extreme cold
Apply dielectric grease to electrical connectors to prevent moisture intrusion
3. Engine Block Heaters and Warm-Up Systems
Before starting, we use:
Engine block heaters
Coolant or oil warmers
Cab pre-heaters to improve operator comfort and reduce idle time
These systems reduce strain during cold starts and protect internal components.
4. Track and Undercarriage Maintenance
Frozen mud and snow can cause buildup around rollers and idlers. We:
Clean undercarriages daily
Inspect for cracked or frozen seals
Use anti-icing sprays on moving parts
5. Cab and Operator Protection
We upgrade:
Heater cores and defrosting systems
Cab insulation and sealing
Wiper blades and washer fluid rated for freezing temps
Comfortable operators work more efficiently — and safely — in cold climates.
Preparing for Hot and Arid Climates
1. Cooling System Optimization
Engines run hotter in high ambient temperatures. We:
Inspect and flush radiators
Use high-temp coolant
Install coolant recovery systems
Ensure radiator fins are free of dust and debris
Overheating is a top cause of failure in hot regions — and it’s preventable.
2. Filtration and Dust Control
In dusty areas (like deserts or quarries), we upgrade:
Engine air filters to heavy-duty dual-stage types
Cabin air filtration systems for operator safety
Fuel and oil filters for fine-particle removal
We also install pre-cleaners to spin out debris before it reaches the air intake.
3. Tire and Track Management
Rubber components break down faster in high heat. We:
Inspect for dry rot or heat-related cracking
Adjust air pressure for temperature fluctuations
Use heat-resistant compounds where possible
In tracked machines, we monitor track tension closely to prevent de-tracking under load.
4. Operator Comfort
For extreme heat, we maintain:
Air conditioning systems
Tinted windows or UV-resistant film
Sun visors and cab fans
Operator safety is key — heat stress can be just as dangerous as machine failure.
Preparing for Wet, Humid, and Coastal Environments
1. Corrosion Protection
Salt, humidity, and rain accelerate corrosion. We protect machines by:
Applying anti-corrosion sprays to exposed metal
Using sealed connectors and marine-grade grease
Washing equipment frequently to remove salt deposits
We also inspect undercarriages and weld points for early signs of rust.
2. Electrical System Sealing
Moisture can short out systems fast. We:
Apply dielectric grease to all terminals
Seal junction boxes and enclosures
Replace damaged boots or gaskets
Moisture-resistant wiring kits can be added to machines in coastal or flood-prone areas.
3. Traction and Drainage Upgrades
On soft or muddy ground, we:
Install aggressive-tread tires or wide pads
Add mud flaps and fender guards
Use raised or sealed undercarriage components when needed
Drainage solutions around fuel caps, hydraulic ports, and vents prevent water ingress during heavy rain.
General Best Practices for All Extreme Conditions
Daily inspections tailored to the climate
Pre-heating or pre-cooling routines before operation
Operator training on environment-specific hazards
Storage in temperature-controlled or covered areas when not in use
Emergency kits including jumper cables, fluids, and recovery tools
We also maintain detailed service logs, enabling pattern tracking and climate-specific scheduling for components that wear faster.
Custom Kits and Retrofits We Offer
To make the process easier, we offer custom climate prep packages:
Winter kits with block heaters, heated mirrors, fuel warmers
Desert kits with enhanced cooling, dust filtration, UV protection
Coastal kits with marine-grade grease, corrosion-proof terminals, and salt spray protection
Battery protection systems, cab climate control upgrades, and undercarriage guards
These kits are tailored for each client based on location, season, and workload.
Final Thoughts: Harsh Doesn’t Have to Mean Hard on Equipment
Harsh environments are tough — but with the right prep, your equipment doesn’t have to suffer. Failing to prepare for climate extremes is a surefire way to shorten equipment life, increase repair frequency, and drive up operating costs.
Through climate-specific maintenance strategies, component upgrades, and regular inspections, we help ensure your machines are ready for anything the environment throws their way.