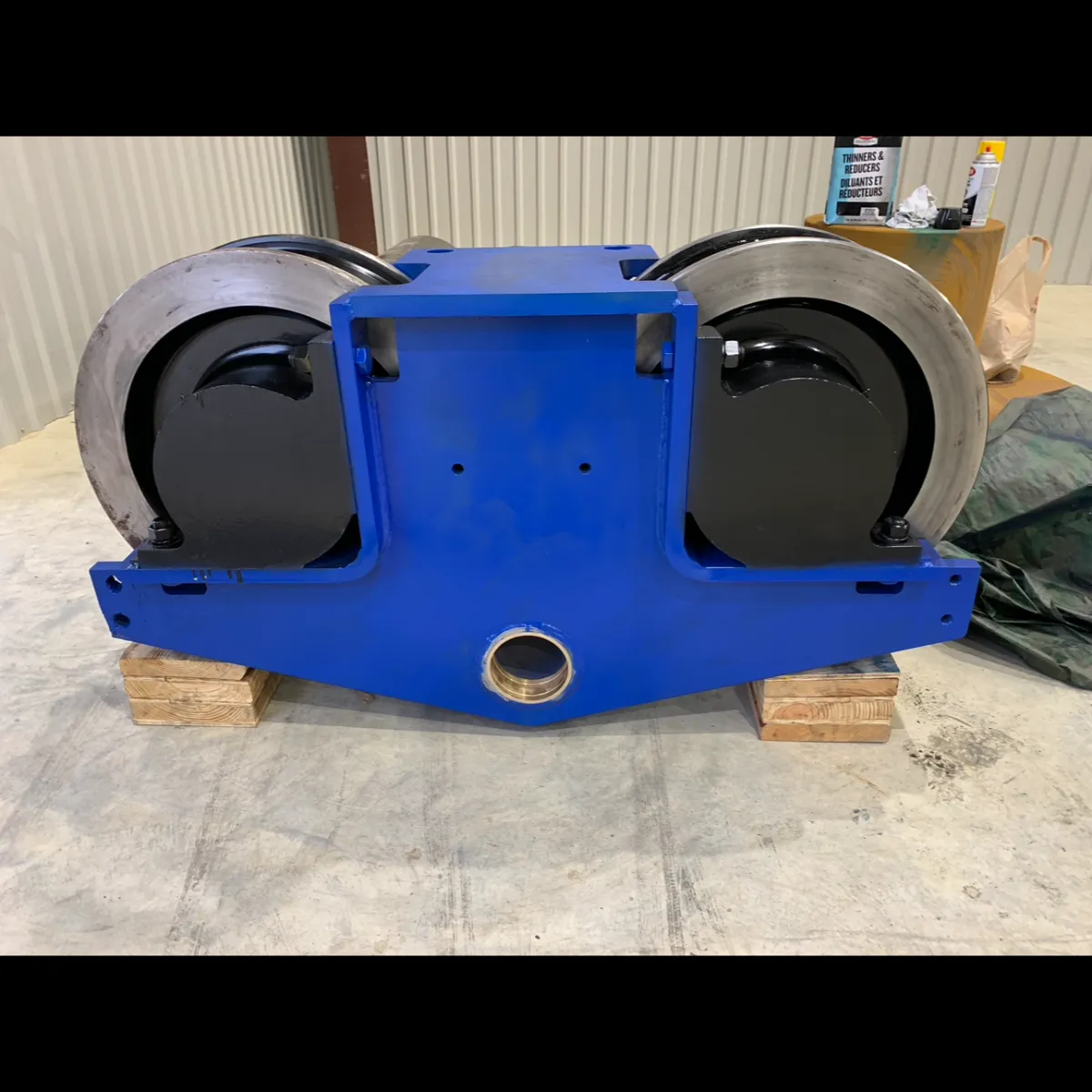
Dealing with Electrical Failures in Harsh Environments
Dealing with Electrical Failures in Harsh Environments: A Practical Guide for Mining and Heavy Equipment
Electrical systems are the nervous system of modern mining and heavy equipment. From ignition and lighting to onboard diagnostics and safety systems, reliable electrical performance is essential for productivity and operator safety. But in harsh environments — such as open-pit mines, underground tunnels, or remote construction sites — these systems are constantly under attack by heat, moisture, dust, vibration, and corrosion.
When an electrical failure occurs, it can halt operations instantly, costing thousands per hour. Worse, it can create safety hazards if key systems like brakes, lighting, or alarms stop functioning. This article explores how to prevent, detect, and deal with electrical failures in harsh environments, especially for those managing mining or heavy-duty equipment.
Why Electrical Failures Are Common in Tough Conditions
Harsh environments accelerate wear and damage on electrical components due to:
Moisture Ingress: Rain, humidity, and water spray can short circuits and corrode wiring.
Vibration and Shock: Constant jolting from rough terrain loosens connectors and damages circuits.
Dust and Debris: Fine particles infiltrate electrical housings, blocking ventilation and causing overheating.
Temperature Extremes: Heat breaks down insulation, while cold can make materials brittle and connections stiff.
Chemical Exposure: Fuel, hydraulic fluid, and grease can degrade seals and connectors over time.
When multiple factors are present — such as in a mining operation during summer storms — failures can happen fast.
Common Electrical Failures in Mining and Construction Equipment
Battery Failures: Poor grounding, cracked cases, or improper charging kill battery life early.
Corroded Connectors: Salt, water, and mud eat away at terminals and reduce conductivity.
Blown Fuses: Sudden surges or shorts can fry circuits, disabling systems unexpectedly.
Wire Harness Damage: Abrasion, pinching, or rodents can damage wiring bundles.
Sensor Malfunctions: High heat or moisture causes sensors to give false readings or shut down.
ECU/Controller Failures: The central computer can fail if not adequately sealed or cooled.
These failures often appear without warning — unless proactive steps are taken.
Preventing Electrical Failures in Harsh Environments
1. Use Sealed Connectors and Weatherproof Components
Replace standard connectors with IP67-rated or military-grade sealed connectors. Use gaskets, O-rings, and dielectric grease to block moisture and dust.
2. Apply Protective Conduit and Harness Wraps
Encapsulate wire bundles in abrasion-resistant conduit or wrap with split loom tubing. In high-vibration zones, secure with rubber grommets to reduce wire fatigue.
3. Relocate or Shield Sensitive Electronics
Mount control modules away from heat or vibration sources, or house them in sealed metal boxes with passive ventilation.
4. Maintain and Test Batteries Regularly
Check terminals for corrosion, test voltage, and clean battery boxes. Use anti-corrosion sprays and make sure ground wires are secure and clean.
5. Use Quality Parts and OEM-Approved Materials
Low-cost wiring or fuses may not meet the heat and current demands of mining environments. Stick to OEM-approved or high-spec aftermarket parts.
6. Add Surge Protection or Voltage Regulators
Voltage spikes are common in large equipment. Add inline surge protection for ECUs and lighting systems.
Diagnosing Electrical Problems in the Field
Step 1: Check the Basics First
Is the battery charged and properly grounded?
Are fuses blown?
Are there any exposed or damaged wires?
Step 2: Use a Multimeter
Measure voltage, resistance, and continuity across terminals. A drop in voltage often reveals where the circuit is failing.
Step 3: Check Connectors and Pins
Disconnect and inspect connectors for corrosion, bent pins, or loose seating. Clean with electrical contact cleaner and reseat firmly.
Step 4: Scan for Fault Codes
Use onboard diagnostics systems like Caterpillar Product Link, Komatsu KOMTRAX, or universal OBD-II readers to pull error codes related to electrical subsystems.
Step 5: Inspect Sensor Functionality
Test sensors with a scan tool or manually compare readings against known standards (e.g., temperature, pressure, or RPM sensors).
Emergency Fixes for Electrical Failures in Harsh Environments
When you're out in the field, miles from a service bay, quick fixes can mean the difference between downtime and delivery.
Temporary Wire Repair: Use waterproof butt connectors, heat-shrink tubing, or electrical tape to seal temporary splices.
Bypass Faulty Circuits: In non-critical systems, bypassing a damaged connector may restore partial functionality.
Field Fuse Replacement: Carry spare fuses in your field kit and know their amperage ratings.
Jump Packs and Battery Boosters: Keep portable power packs to restart dead machines.
Moisture Removal: Use compressed air and heat guns to dry flooded connectors or fuse panels.
Creating an Electrical Maintenance Checklist
For consistent performance in harsh environments, integrate electrical checks into your daily or weekly maintenance plan.
Sample Electrical Maintenance Tasks:
Check battery voltage and connections
Clean and inspect fuses and fuse holders
Inspect wiring harnesses for abrasion
Test lights, horns, and warning systems
Use diagnostic scan tools monthly
Confirm ECU enclosures are sealed
Replace worn grommets and cracked conduit
Digital tools like CMMS (Computerized Maintenance Management Systems) can help log, schedule, and track these inspections across your fleet.
Investing in Training and Awareness
A well-trained operator or technician is your first line of defense. Make sure your team knows:
What warning signs to look for (flickering lights, electrical smells, system resets)
How to complete a visual wiring inspection
The safe way to disconnect power sources before working on equipment
When to escalate to a certified electrician or OEM service provider
Even a 30-minute toolbox talk on electrical failure signs can prevent serious outages.
Final Thoughts: Stay Connected and Operational
Dealing with electrical failures in harsh environments isn’t just about putting out fires — it’s about preventing them in the first place. With the right components, consistent inspections, and trained personnel, your equipment can maintain electrical integrity even in the most extreme conditions.
From open-pit mines in Georgia to underground tunnels in remote regions, electrical system reliability is key to staying productive, profitable, and safe.