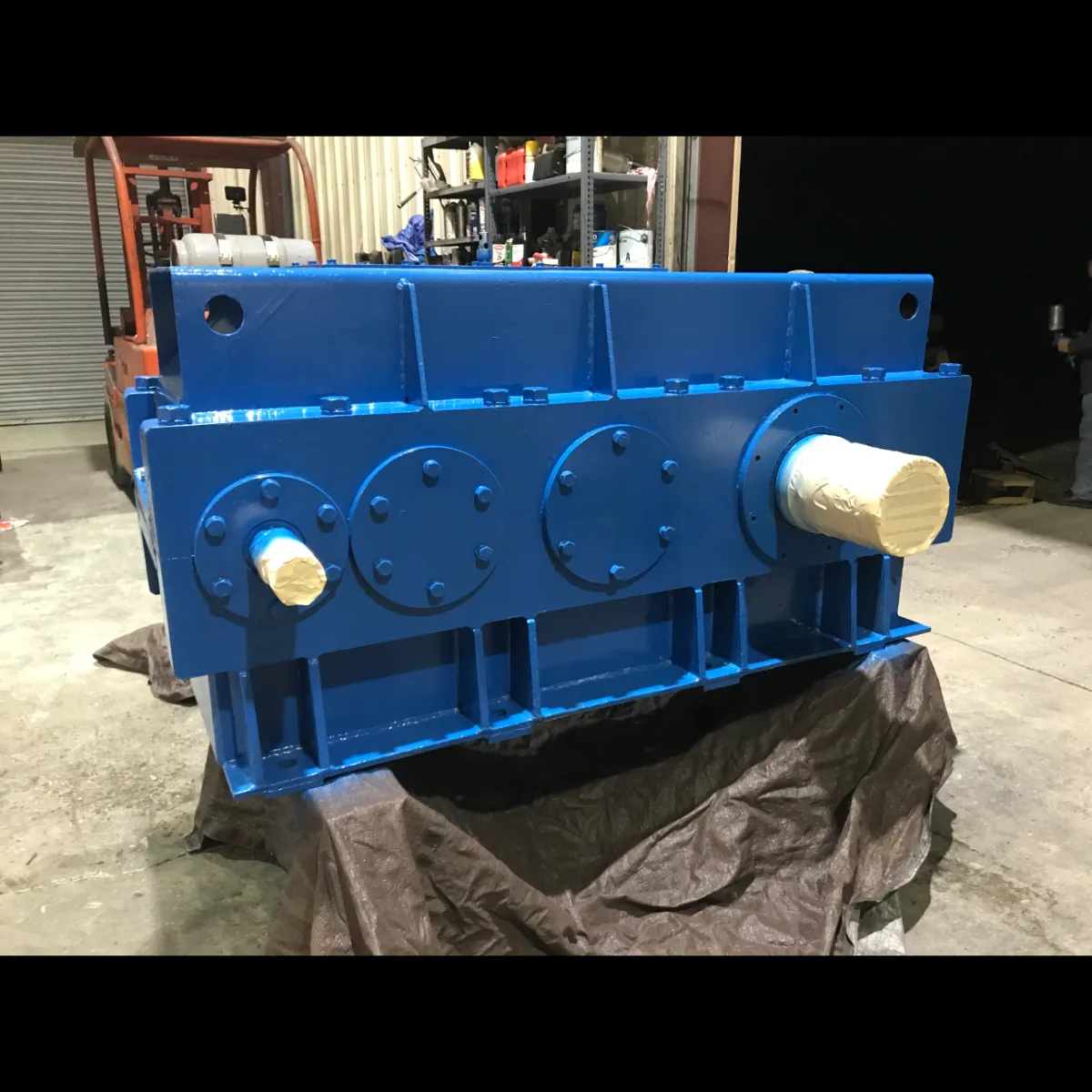
A Beginner’s Guide to Preventive Mining Equipment Care
A Beginner’s Guide to Preventive Mining Equipment Care
In the mining industry, where heavy machinery operates under intense pressure and environmental stress, equipment reliability is everything. One unexpected breakdown can cause thousands in losses per hour. That’s why understanding and applying preventive maintenance (PM) practices is crucial — especially for new operators, technicians, or maintenance managers just starting out.
This beginner-friendly guide will break down the fundamentals of preventive mining equipment care, helping you extend the lifespan of your machinery, improve safety, and reduce operating costs.
What Is Preventive Maintenance in Mining?
Preventive maintenance is the proactive servicing of equipment at regular intervals to avoid unexpected failures. It includes scheduled inspections, part replacements, lubrication, fluid changes, and software checks — all done before a breakdown occurs.
The main goal is simple: keep your equipment running smoothly and avoid unplanned downtime.
Why Preventive Maintenance Matters
Mining equipment works harder than most machinery. Excavators, haul trucks, crushers, drills, and loaders deal with:
Abrasive materials like granite or gravel
Extreme heat, moisture, and dust
Long shifts and heavy loads
Vibrations, pressure, and constant movement
Without preventive care, these machines are at high risk of failure, which can lead to:
Lost productivity
Emergency repair costs
Safety hazards
Reduced machine lifespan
A small investment in regular maintenance can prevent massive repair bills and costly work stoppages.
The 4 Types of Preventive Maintenance Tasks
Time-Based Maintenance
Performed after a certain number of days, weeks, or months. Example: Replacing air filters every 60 days.Usage-Based Maintenance
Scheduled based on run-time hours or mileage. Example: Changing engine oil every 250 operating hours.Condition-Based Maintenance
Triggered by sensor readings like temperature, pressure, or vibration. Example: Replacing hydraulic hoses when a pressure drop is detected.Predictive Maintenance
Uses machine learning or smart diagnostics to predict failure before it happens. Example: Using Caterpillar’s Product Link or Komatsu’s KOMTRAX data to detect early wear.
For beginners, time-based and usage-based maintenance are the most common starting points.
Common Preventive Tasks for Mining Equipment
A beginner’s mining equipment maintenance checklist typically includes:
Lubrication: Grease joints, bearings, and moving parts to reduce friction.
Fluid Checks: Inspect and top off engine oil, coolant, transmission fluid, and hydraulic oil.
Filter Replacements: Change air, fuel, oil, and hydraulic filters at recommended intervals.
Hose and Belt Inspections: Look for cracks, fraying, or leaks.
Battery Testing: Check voltage, corrosion, and secure mounts.
Tire and Track Inspections: Ensure proper inflation, wear levels, and alignment.
Brake and Clutch Checks: Essential for safe stopping power.
Bucket and Attachment Checks: Look for worn teeth, cracks, and loose pins.
Electrical System Scan: Test lights, sensors, fuses, and warning indicators.
Software Updates: Ensure onboard diagnostics and telematics are up to date.
How to Build a Preventive Maintenance Schedule
Step 1: List All Equipment
Create an inventory of every machine, its model, and manufacturer.
Step 2: Find OEM Recommendations
Check the operator’s manual or manufacturer website for maintenance intervals and service tasks.
Step 3: Log Machine Hours
Use hour meters, telematics, or manual logs to track equipment usage.
Step 4: Create a Maintenance Calendar
Use spreadsheets, a whiteboard, or software like CMMS (Computerized Maintenance Management Systems) to map out recurring tasks.
Step 5: Assign Responsibilities
Define who performs inspections, fills out reports, and schedules service.
Step 6: Track and Adjust
Log completed maintenance and monitor equipment performance. Adjust intervals if wear appears earlier than expected.
Tools That Help With Preventive Maintenance
CMMS Software (e.g., eMaint, Fiix, or UpKeep): Automates task scheduling and logs service history.
Telematics Systems (e.g., JDLink, Product Link, KOMTRAX): Tracks machine health and sends alerts.
Mobile Inspection Apps: Allows field operators to complete checklists via tablet or phone.
Parts Inventory Management: Keeps essential replacement parts on hand to reduce delays.
Beginner Mistakes to Avoid
Skipping Daily Inspections: A quick pre-shift walkaround can catch leaks or cracks early.
Using the Wrong Lubricants or Fluids: Always use OEM-specified products.
Ignoring Warning Lights: Dash indicators are there for a reason — don’t disable or ignore them.
Delaying Filter Changes: Clogged filters cause performance issues and damage internal systems.
Failing to Record Maintenance: If it’s not written down, it didn’t happen. Keep organized records.
Benefits of Preventive Mining Equipment Care
✅ Fewer Emergency Repairs
Catch issues before they escalate.
✅ Longer Equipment Life
Reduce wear on high-value machines.
✅ Lower Operating Costs
Avoid inflated emergency service rates.
✅ Improved Worker Safety
Fewer breakdowns mean safer job sites.
✅ Higher Equipment Availability
Less downtime = more productivity.
✅ Stronger Compliance
Meet industry safety and maintenance standards.
Getting Started as a New Operator or Technician
Review Equipment Manuals: Know your machines inside and out.
Ask Questions: Learn from senior technicians or supervisors.
Use Checklists: Don’t rely on memory. Use written or digital forms.
Stay Consistent: Preventive care is about routine, not convenience.
Keep Learning: New tools, diagnostics, and software are always emerging.
Final Thoughts: Preventive Care = Profitable Mining
Preventive mining equipment care isn’t just for large-scale operations — even small mining businesses benefit from consistency and attention to detail. For beginners, the key is starting small, being consistent, and learning from your data. Over time, you’ll gain experience and refine your plan to match your fleet and production goals.