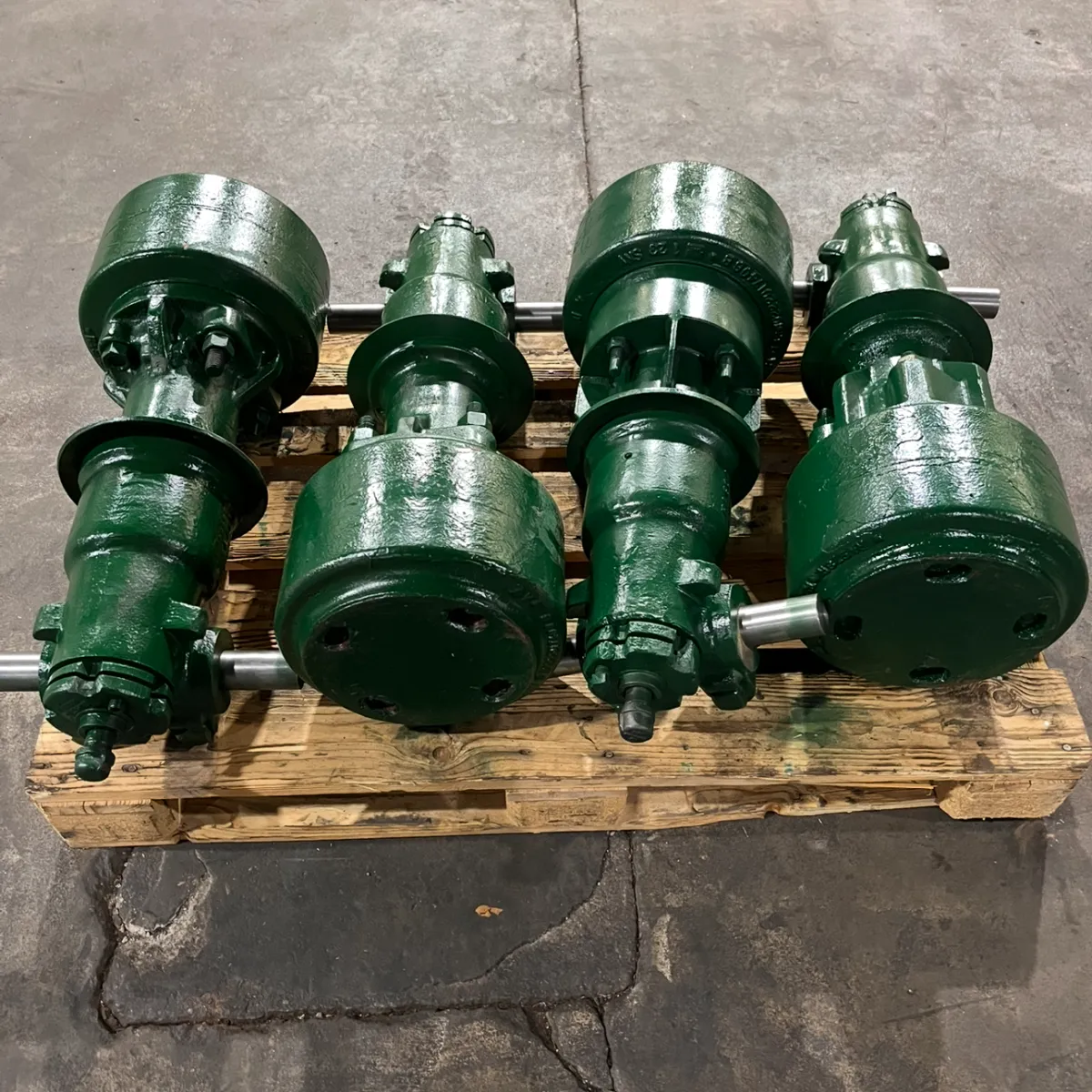
5 Things to Check Before Calling a Mining Repair Tech
5 Things to Check Before Calling a Mining Repair Tech
When mining equipment breaks down, the instinct is often to call a technician immediately. However, before you reach for the phone, performing a few critical checks can save time, prevent unnecessary expenses, and minimize operational downtime. Whether you operate a haul truck, dozer, crusher, or underground loader, understanding your equipment's behavior is key to efficient maintenance.
Below are five important things to check before you contact a mining equipment repair technician — all based on industry best practices and technical know-how.
1. Perform a Visual Inspection of the Equipment
Visual inspections can reveal a lot about a machine’s condition. Always check for:
Leaks (hydraulic fluid, oil, fuel) — For more on common fluid leak issues, check Caterpillar's maintenance tips.
Rust or corrosion around joints and electrical panels.
Loose or missing bolts on attachments, undercarriages, or lift systems.
Frayed wiring or exposed circuits that may indicate electrical problems.
Cracked welds in high-stress areas like booms or buckets.
Use your smartphone to snap photos of any visible issues — these visuals can help a technician diagnose problems faster, and reduce costly guesswork on-site.
2. Check Warning Lights and Diagnostic Codes
Many modern machines come equipped with onboard diagnostic systems that alert operators to internal issues before failure occurs. Here’s what to do:
Review the fault codes in the operator display.
Check pressure gauges, temperature indicators, and error symbols.
If available, connect an OBD or CAN-bus reader compatible with your equipment (like those used by Komatsu or Volvo CE).
Record fault codes or messages. These systems often store alerts briefly and may reset when the ignition is cycled. Don’t let the data disappear.
3. Inspect Fluid Levels and Filters
Fluids are the lifeblood of mining machines. Insufficient or contaminated fluids are one of the most common culprits behind system warnings. Focus on:
Hydraulic fluid levels and clarity. Reference Shell’s guide to hydraulic oils for more on fluid specs.
Engine oil, especially for signs of metal shavings or a burnt odor.
Coolant level, color, and temperature stability.
Transmission and differential fluids, especially in machines operating on inclines.
Clogged filters or dirty reservoirs can cause overheating, erratic controls, or sluggish hydraulics. Replacing a $50 filter could prevent a $5,000 repair.
4. Review Maintenance Logs
One of the most overlooked yet important steps is to consult your maintenance history. Many service issues stem from overdue inspections or neglected maintenance.
When was the machine last serviced?
Are any parts or fluids past their replacement interval?
Were any temporary fixes made in the last service?
Using digital fleet management tools like Fleetio or EMaint CMMS makes tracking these issues easier and can even help automate preventive scheduling.
Your repair technician will appreciate any records — even a simple spreadsheet — as it could steer them directly to a likely cause.
5. Evaluate Recent Equipment Use
Before assuming mechanical failure, consider operator behavior or abnormal working conditions. Ask:
Was the machine recently used for tasks outside its typical duty?
Was it working on sloped, unstable, or abrasive terrain?
Were any new attachments or implements used recently?
Were operators trained and following correct startup/shutdown procedures?
Small issues, such as running hydraulic attachments without disengaging them, overloading the bucket, or operating with incorrect tire pressure, can all mimic major failure symptoms. Resolving these issues early prevents repeat calls and builds a proactive repair culture.
Bonus: When You Do Call, Be Prepared
If these checks don’t resolve the issue, it’s time to call a professional. But to save money and time, provide the technician with:
Machine make, model, and year
Any warning lights or codes observed
What symptoms are present (noises, smells, performance loss)
Photos, videos, and fluid condition notes
Maintenance history
Companies like Epiroc, Holt CAT, or regional players in Atlanta can often prep their team better when they know what they’re walking into — especially if your mining site is remote or high-demand.
Conclusion: Awareness = Uptime
Performing these simple steps before you call a mining equipment repair tech ensures your equipment is understood, your technician is prepared, and your downtime is minimized. Every hour saved means higher efficiency and profit for your operation.
Whether you run a quarry in Atlanta or a sand mine in Savannah, routine awareness and preventive troubleshooting play a key role in maintaining long-term performance. For businesses seeking Mining Equipment Repairs in Atlanta, GA, choose a provider that values transparency, speed, and knowledge-backed service.
Ready to schedule service? Contact our expert repair team here and get your machines back on the job.